
Skeleton launching a fully automated supercapacitor production line
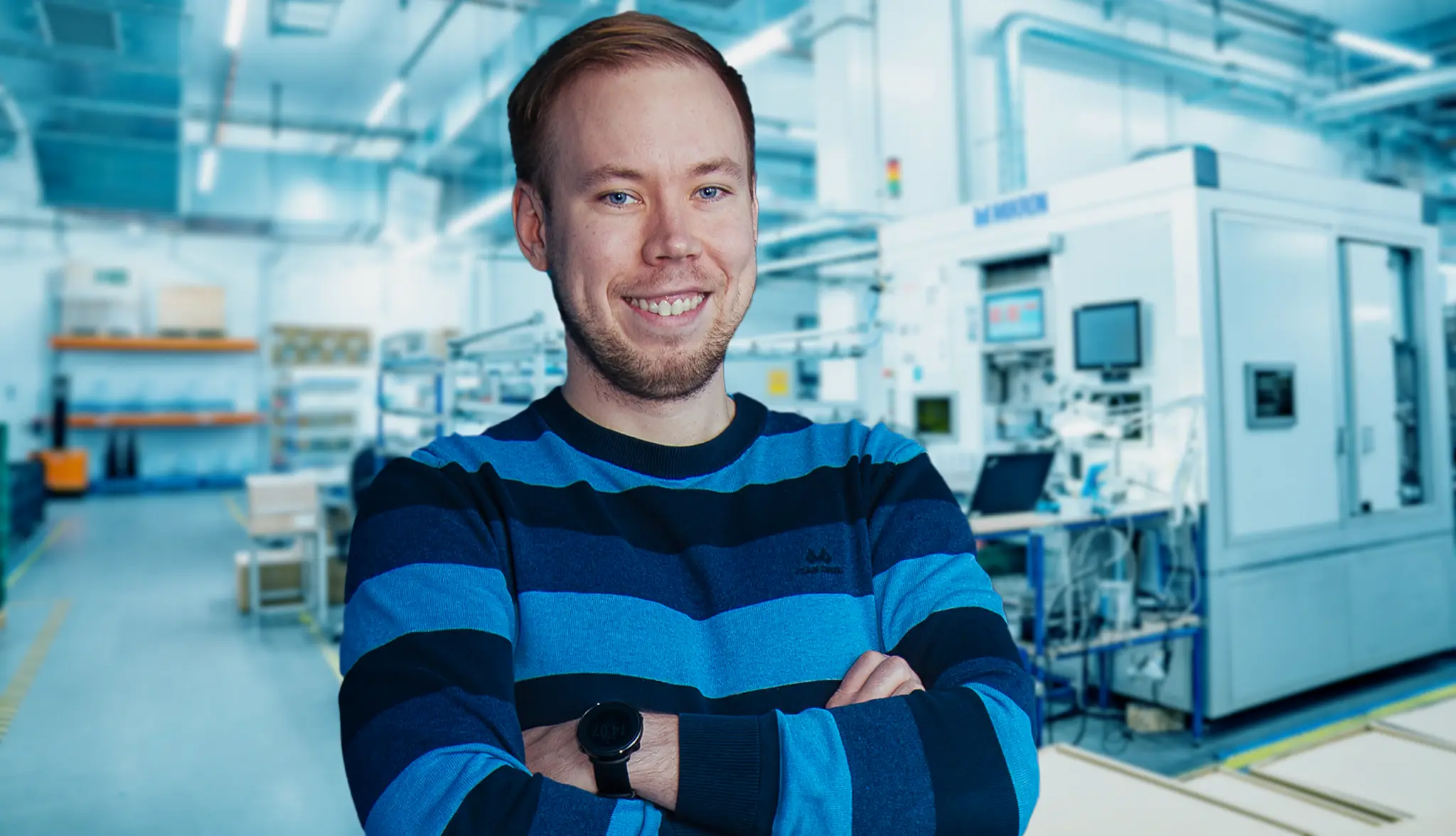
We’re building the world’s largest and most modern supercapacitor factory in Saxony, Germany. The first-of-its-kind Leipzig Superfactory will include the inaugural fully automated supercapacitor production line.
With the expected Start-Of-Production in 2024, construction is already underway for Leipzig Superfactory. Designed in cooperation with Siemens Digital Industries, it will increase Skeleton’s production capacity 40-fold, allowing us to meet the increasing demand from electrification and decarbonization projects globally.
Skeleton Technologies’ objective is to make its energy storage devices more affordable. The economies of scale provided by this new technology, combined with the use of our patented Curved Graphene raw material, will dramatically drive the production costs down, boosting the competitiveness of supercapacitors as the key enabling technology for the future of electrification. After the completion of the 5-year scale-up project, production costs are expected to lower by almost 90%
The current one-sided coating line (35 m) at the Dresden Superfactory
Leading the automation of supercapacitor production
“Globally, only islands of automation are used at supercapacitor production sites. While the individual processes are automated, these islands of automation are separated by manual assembly and transport,” said Skeleton’s Scale Up Equipment Launch Manager Taavi Pärtin. Despite sharing commonalities with other energy storage devices like lithium-ion batteries, supercapacitor production is not as evolved due to its youth and around 50 times smaller market size.
"Globally, only islands of automation are used at supercapacitor production sites."
Supercapacitor production consists of five main steps from electrode coating to cell testing. Let’s look at the first step to get a better understanding of the difference between semi-automated and automated production.
1. Electrode manufacturing (mixing, coating, calendering, slitting)
2. Jellyroll winding
3. Roll-to-Cell assembly
4. Cell filling and closing
5. Cell testing
“Current electrode production is accomplished by a partially automated coating line that gives feedback on product quality, but still requires permanent operator attention as well as diligent supervision of the product tracking system,” explains Taavi Pärtin. In addition, some quality tests must be conducted off-line, delaying feedback and corrective actions to the production operations.
The electrode is only coated on one side and rolls must be brought back to the beginning of the line to be coated from the second side. In fully automated cell production, electrode production will still be based on wet coating techniques, but the implementation of a novel coating technique enables double-side coating that would half the throughput time per meter.
The automated line will utilize machine learning and in a later stage artificial intelligence to link quality control systems (coating thickness measurement by β-rays, coating width control by high-quality imaging techniques, humidity sensing by IR sensors) with production process control adjustments (coating head settings, drying oven settings). This link will result in automatic corrections, superior quality, and a more efficient production.
In electrode calendaring and slitting, the respective electrode rolls will be recognized by radio-frequency identification (RFID) technology, automatically adjusting machine settings as needed and leaving a clearly traceable product through all steps. Hand-over of slit electrodes to cell production processes will be machine directed with the option of being fully automated.
"All manual inspection steps are removed and replaced with automatic processes."
Cell assembly, filling and electrical testing production steps are fully automatic and do not require operator influence. “A big upgrade from the current cell production is that all manual inspection steps are removed and replaced with automatic processes that are faster and more reliable,” adds Taavi Pärtin.